
Figure 4 shows the relative power consumed by a lubricated screw compressor with varying system storage sizes at different part load percentages. If the compressor in question is operating at part load in load/unload trim duty, a special kind of calculation is required to determine the specific power that takes the effective storage receiver capacity of the system into account. In additional to this the lower pressure will cause unregulated compressed air flows to reduce resulting in even more savings of about 0.9% for every psi reduced. The resulting 9.5% reduction would reduce the total 10-year power costs significantly. Its lower specific power number illustrates the savings potential if you operated your air compressor at 100 psi rather than 125 psi. For some VSD-controlled machines, the lower pressure my result in the same power consumption but more cfm output through automatically programmed increases in maximum speed.Īn additional item has been placed in Figure 3 as Item E for interesting comparison a 100-psi rated compressor.

Lower than rated operating pressure results lower kW consumption for fixed speed compressors. Manufacturers should be consulted to provide assistance finding out the actual package kW consumption at the chosen pressure. The numbers would have to be adjusted for a common pressure by about 1% for every 2 psi increase in pressure to compare fairly. Because two of the manufacturers have chosen to test their compressors at 115 psi this lower pressure results in lower specific power numbers by about 5%. Note that Figure 3 is not an exact apples-to-apples comparison. Fortunately, CAGI Compressor Data Sheets are now readily available from participating manufacturers that show compressor and air dryer energy consumption in a standard format.įigure 3: Specific power can vary between makes and models (various selected CAGI members)
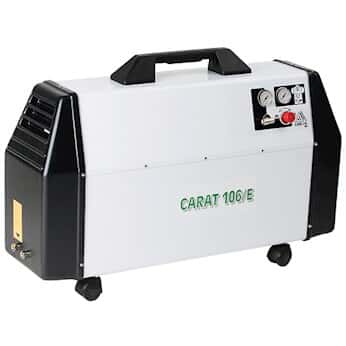
In past, information about air compressors was based on a variety of test conditions, but much of it was confusing and conflicting. This can help you make appropriate decisions about energy efficiency. To do adequate power cost calculations some accurate and consistent information is needed so that true costs can be calculated. Because of this even a 5% change in operating efficiency can save you $18,500 in electrical costs over 10 years. Over a 10-year period, these costs can represent about 76% or more of the total life cycle cost of the air compressor, with the purchase price representing only 12%. The price of various compressor brands and models may differ by only a few hundred dollars, making the cheapest machine the obvious choice to the purchasing department, but examining energy characteristics can reveal additional hidden costs.Ī 100-hp compressor requires about $37,000 in annual electrical costs at 10 cents per kWh with a five-day, two-shift operation of about 4200 hours per year.
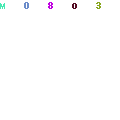
Figure 1: The 10 year operating cost of a typical air compressor is mostly energy (Compressed Air Challenge, There is more to the purchasing decision than the initial first cost.
